
Case Studies
The selected case studies represent only a few examples of KeSan's tooling and molding services and how they
have helped our customers resolve challenges and move product to market. It is intended to provide a comprehensive
guide of our specialties.
Read about how companies like yours are profiting from KeSan:
- Case 1: automotive component
- Case 2: medical device
- Case 3: consumer electronics
- Case 4: multi-cavity
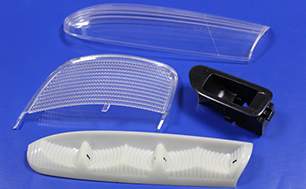
Part name: Befestigungslasche
Application: motorcycle oil system
General tolerances: DIN ISO 2768MK, DIN ISO 13715
Challenges: intricate parting lines
cut cost
blow molded with aluminum oil tank
short lead-time
angular multiple slide
impact-modified plastic material, shrinkage unknown
The customer was looking for:
• a quality manufacturing arm to produce high-liability products
• previous experience with automotive parts
• functional tools building within short term
• engineering and tooling support
This part was designed to be inserted with blow molded aluminum tank, no sharp edges and angles were allowed for this purpose. The blow molded part should be easily separable for recycling purposes and friendly to environment; unmolding agents were forbidden. An impact-modified non-reinforced Durethan PA was chosen for its heat- and chemical- resistance, as well as high MFI (melt flow index). This fastening lug part was injection molded on a 350-ton HaiTian press. The schedule was a tight one; our team built mold and produced parts within 5 weeks. KeSan achieved this mould within the planned finance and time budgets.
Project name: Inter-Vial
Application: a reconstitution device
General tolerances: ISO 2768-F
Challenges: clean room molding tools
100% automation
cut cost
short lead-time
un-screwing mechanism
two-stage ejection
three-plate molds
Our customer was looking for:
• a quality manufacturing arm to produce high-liability products
• previous experience with medical products
• build functional tools within short term
• technical molds tooling center
A 6 cavities family mold was built firstly, and parts were submitted to customer for functional and structural tests. Production tools featured in unscrewing mechanism, three-plate mold, and two-stage ejection. The tri-angle outer shape of two shells assembly made the screwing orientation difficult; KeSan achieved a perfection assembly for the two parts.
Project name: 961#1, 962#2, 966#1, 712#2, 977#3, 977#4, 977#5
Application: ITW Chip Holder
General tolerances: ISO 2768-F
Challenges: cut cost
lean manufacturing
erowa workholding system
very short lead times
Our customer was looking for:
• lean manufacturing center in China
• functional tools building within short term
• tooling with strict quality management
• good engineering support
KeSan was selected for the quality precision manufacturing capacity to supply precision cavity and core inserts and mold tooling. The general tolerance of the workpiece was +/-0.0004”, every small red copper electrode was vital for EDM machining by Agie Charmille and EROWA system taking VDI 3400/18#, for each piece should be interchangeable. Every workpiece was double inspected by our CMM machines before putting into use, which had greatly enhanced our work efficiency afterward. Kesan achieved this project by the strict quality management system.
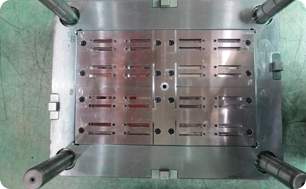
Part name: Bracket
Application: TV interior part
Challenges: 32 cavities
short lead-time
cut cost
self-degate
Our customer was looking for:
• previous experience in multi-cavity tooling
• functional tools building within short term
• cost-effective solution
• engineering support on injection and ejection systems
Our customer wanted to save cost on hot runner system, while keeping 32 cavities to meet a high production demands, every cavity was an individual insert for future maintenance and replacing work. A short cycle time was pursued by placing efficient and reasonable cooling system. The tool was designed with complete self de-gating, while PS plastics made the gate runner break easily before ejection, the gate scraps covered the impression. Our engineer solved this problem by adding ribs on gate ends, which could help gate stay with parts during ejection. A cold runner system was applied to replace the hot runner system. KeSan helped our customer reduce cost by 15% while building a functional mold.
